An overview
– Part 4 –
We would like to suggest a different approach that promulgates that lean management implementation should begin at the microlevel; if a lean management project is to be implemented only for a specific area, then the definition of “senior management” will turn out to be the “senior management of the specific area where the implementation is conducted.” A holistic approach that should be connected to the larger context will rather be a process/unit/department that takes improvement steps, in the context of a larger cluster of departments or the institution. Communication and problem solving will be simple and fast at this level, where mid-level managers have to supervise their dedicated areas, compared with institutional implementation where the CEOs or Chief Medical Officers have to address a myriad of problems overarching the institution. Finally, the customers (patients) of a specific division may have unique characteristics that may not be shared by other patients seen in the institution.
As previously mentioned, resistance to changes is driven in most companies by lack of executive support. However, following a bottom-to-top approach will redefine the responsibility of the institution’s senior management to three main strategic areas; rather than committing a large amount of time and energy to the lean process, senior managers should:
- Identify the “vital few” areas that will benefit most from implementing lean. Therefore, the Pareto Principle will be applied identifying the 20% areas that will provide 80% of institutional benefits allowing the organization to maximize the return on investment (ROI).
- Be committed to allocate the supporting resources necessary for the required changes, and, in turn, the area managers will be solely in charge of the process and periodically communicating progress.
- Be in charge to ensure effectively communicating the results of the changes to the stakeholders in the organization, especially those who are not participating in, or affected by, the lean management process. This approach will be also instrumental in institutional cultural change, allowing managers in areas that did not implement lean to observe the benefits incurred at all levels.
Rather than concentrating only on operational aspects of lean management thinking, managers at the departmental/unit level will be able to reconcile operations with socio-technical aspects that respect the “human system,” i.e. take into consideration the effects of the changes on the employees with whom they have daily interactions. Therefore, in order to create “cumulative capabilities” and value, managers at all levels need to realize that their job is not only improving the processes, but developing the departmental job-force that ultimately is in charge of the implementation.
Example of Lean Management Implementation at an Academic Healthcare Institution
Case Western Reserve University School of Dental Medicine (SODM) is located in Cleveland, Ohio and enrolls yearly around 70 students who participate in a 4-year rigorous academic program towards the dental doctoral DMD degree. Clinical training includes third-and fourth-year students providing dental care; the DMD clinic has 143 operatories in which students treat yearly over 8,000 patients throughout over 30,000 encounters. In addition the school has 75 simulation operatories in which first-and second-year students learn clinical procedures on mannequins.
Being an institution that integrates academic education with patient care, one has to define the following customer groups:
- Students, “primary customers”—who pay tuition and therefore are a source of revenue
- Patients, “primary customers”—who pay a (reduced) fee for dental treatments
- Faculty and staff—“secondary customers,” considered by the school as “internal customers” and will be influenced by any changes in processes and policies
Such institutions are in a unique situation because they have more than one group constituting the “primary customers.” In the United States, dental schools are also guided by standards published by the Commission on Dental Accreditation (CODA); these standards do not allude directly to lean management strategies but contain statements regarding the obligation to implement “continuous quality improvement” at all levels, quality assurance systems that include cycles of “Plan, Do, Check, Act,” and evaluation and application of new technologies.
It is beyond the scope of this article to present all the tools that support the lean management concept; these are presented in great detail in several publications. We present an example of implementation of a new technology in the DMD clinic that illustrates use of some lean instruments.
Contact BHM Today
This concludes the fourth and final part of Lean Management for Healthcare Organizations. If you’d like to learn more about lean management and how it can benefit your organization, contact the experts at BHM Healthcare Solutions today.
Email: re*****@*******pc.com
Phone: 1-888-831-1171
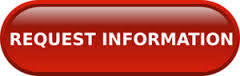
The complete article, Lean Management—The Journey from Toyota to Healthcare (©2013 Teich and Faddoul), is available online at https://www.ncbi.nlm.nih.gov/pmc/articles/PMC3678835/
The National Center for Biotechnology Information advances science and health by providing access to biomedical and genomic information.